Persico constantly focuses on the design and production of innovative automated manufacturing systems for advanced material processing.
Through our long experience as a provider of a full range of services, from concept to prototype manufacturing, we have learned how to optimize the processes and the efficiency of our automatic lines.
Choosing Persico production lines means:
- Cycle time reduction
- Worker efficiency
- Energy saving
- Different processes integrated into a single production line
- Factory footprint minimization
- Process control
Over the years, Persico has supplied the market with numerous projects involving different technologies, including moulds, machinery and full automation. Our production lines are designed by our technical teams and built by our production teams. Moreover, our customers are constantly supported by our process engineering teams for codesign and R&D activities.
As a production line provider, Persico boasts a wide portfolio of standard and customized solutions using different state-of-the-art technologies.
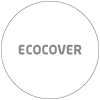
Automotive production lines
Persico can supply full production systems for vehicle components:
VEHICLE INTERIOR LINES
- Instrument panels and centre consoles
- Door panels and seatbacks
- Headliners and pillars
- Parcel shelves and load floors
VEHICLE NVH LINES
- Trunk side, carpet and wheelarches
- Battery covers, underbodies and engine insulations
- Heat shields
VEHICLE LIGHTWEIGHT COMPOSITE LINES
- Bulkheads, roofs, bumpers, hoods and composite car parts

Highly efficient one-step covering and edge folding machine The best high-quality covering process for TPO and PVC foil
Discover how to save material with True Shape precision technology.
True Shape’s numerous productivity advantages
- Material saving
- One-step solution
- High speed
- Turnkey process
- Flexible system
- Mass production
- Energy saving
- Complex part processing
- Precision results
- Automated process
Unsurpassed results with countless materials
NFPP, leather, fake leather, PU, PVC, TPO, PU foam, glass fibre, paper, fabric, nonwovens, Alcantara and more.
Ideal for vehicle interior parts
- Instrument panels
- Centre consoles
- Door panels
- Seatbacks
- Headliners
- Pillars
Persico’s ONE-STEP INTEGRATED SOLUTIONS with edge folding
- Covering + Edge folding
- Edge folding + Assembling
- Laminating + Edge folding
- Gluing + Edge folding
Let us create your CUSTOMIZED SOLUTIONS with our innovative technology portfolio.
- Pinch trimming
- Bypass punching
- Saw cut
- SkillCut®
- Painting
- Spraying
- Thermal oil conditioning
- Water conditioning
- Electrical heating
- Infrared (IR) heating
- Hot air heating
- Ultrasonic (US) welding
- Infrared (IR) welding
- Gluing

A new spray skin process
Drastic reduction in dead time.
Persico Automotive has developed EcoCover, a new spray skin process that achieves amazing results in a wide range of colours. It can even create faux stitching! During the EcoCover process, a release agent is first applied to the mould. Then, using in-mould coating, the paint is sprayed on, followed by a polyurethane (PU) material. The technique creates lightweight leather-like skins and allows for design freedom and extremely small positive radii. Thanks to the PU, the pieces have a pleasant feel and do not become brittle at low temperatures. Additional benefits of the process are very long tool life, material savings and lower energy usage. Persico offers full production systems for dashboard instrument panels. In addition to the EcoCover process, we can provide skin cutting SYSTEMS, back-foaming TOOLS (in partnership with WIS Tooling) and TOOL CARRIERS, and punching tools and machines. Persico Automotive has collaborated with Hennecke GmbH on testing the innovative EcoCover process.
EcoCover Pilot Plant / Prototype Area
Key Features
20 full instrument panels per day
Climate-controlled booths with full control of temperature and relative humidity
Manual trolley movement that can be easily automated
Manual tool cleaning area
Material storage and preparation area
Key Benefits
PU material → NO PVC → NO brittleness at low temperatures + NO plasticizer migration due to ageing and NO visible airbag cut line after 6-7 years
Design freedom
Extremely small radii
More pleasant feel
Lightweight → over 20% less weight
Lower material cost (very thin aliphatic PU layer)
Little run-off
Very long tool life
Machine-block tools possible
Very long tool life
Machine-block tools possible
Easy multi-colour masking
Low energy consumption
Steps
Release Agent Application
Manual application in pilot plant
Automatic robotic electrostatic application on production line
In-mould coating (IMC) with Aliphatic PU
UV-stable / long-term durability
Accurate hardness and haptics settings
Wide range of matt and glossy colours
Flash-off
Aromatic PU spraying
Less density
Lower cost
Perfect back-foam interface
Hennecke PU-Spray System
Start and stop technology → NO over-spray
Air-supported high-pressure spray technology
Homogeneous thickness
Curing
Manual Demoulding